Zigler’s new technology
Can you tell me about any recent technology and innovations from Zigler – particularly in terms of its sorting system for BOV inserting?
"As we are all looking for sustainable solutions due to the global situation, we all need to look for effective, time-saving ways to keep production stable. BOV production is evolving, and our customers are looking for more and more automated solutions to avoid the interruption of work – due to the employee’s absence, or simply not being available to work."
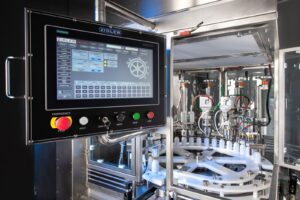
What has the development journey of this technology been like?
"Firstly, it came from the demand of pharmaceutical device producers, who wanted to avoid other points of contamination, and so they asked for sorting and feeding equipment. Initially we tested BOV via our extant systems, but we quickly realised these types of valves are delicate and easy to reap off from the top part – so we had to look for other ways of handling. This led to our dedicated BOV equipment, which safely unscramble and deliver the BOV into an aerosol can.
"A video featuring these machines can be watched by following this link: vimeo.com/717438803"
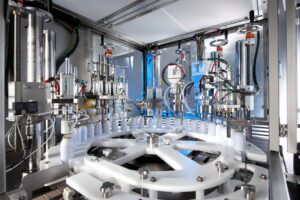
What do you feel are the most significant issues facing EU producers?
"Global deglobalisation... the process of diminishing interdependence is a must. We observe that not everything is available 24/7 anymore, and one cannot outsource as cheaply before the pandemic, with workers not as dedicated to work as they used to be. Employees are searching for less time-consuming jobs, giving them more free time – and there are many more financial, tax and political issues in play."
In 2013, a department was established at ZIGLER to develop equipment for the pharmaceutical industry. Does pharmaceuticals form a major part of the business now?
"No, it is a strong, well-rounded market but still not a major one for aerosols. We are working with our potential customers and our laboratory team to find solutions suitable for them to develop this field."
Zigler’s machines are used in 40 countries across the world. What do you feel customers value most about your service?
"We work closely with our customers. Our goal is to provide long-term cooperation and wide support for our business partners – which is what we prefer to call our customers. Their being successful is our success. We always consider their needs, plans and potential risk points, reaching from our experience to land them in a safe environment to work, and to come back to us for more."

Similarly, each line is built to specification. How do you work with customers to ensure you are meeting their needs?
"We ask a lot and listen. Very often we spend months on the development stage. Our team is constantly revising old and new solutions and looking for better ones."
What do you feel is Zigler’s greatest achievement so far?
"The trust of our customers keeps them coming back for more equipment, resulting in mutual growth."
What does 2023 hold for Zigler?
"Who knows: I think we all are asking ourselves this question! Hopefully more good projects and a strong work–life balance."
As featured in the last edition of World Aerosols magazine, viewable here.