CosterEco “enhances aerosol transition to compressed gases”
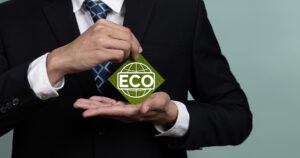
Transitioning from liquefied propellants towards compressed gases brings improvement to the sustainability, safety, and costs of traditional aerosols, and helps meet the growing consumer demand for natural products, according to Coster, adding that sustainability is a fundamental pillar of its business.
Compressed gases, such as nitrogen and air are low in toxicity, non-flammable and natural and make an ideal propellant for aerosol products if it wasn’t for the performance gap compared to LPG-filled ones, said the organisation.
Employing a non-fossil sourced propellant can bring significant reductions to the CO2 footprint.
Aerosols filled with compressed gases suffer from performance variance (such as delivery rate) due to the pressure drop during the lifetime of the product, whereas with LPGs, a constant pressure is maintained inside the can, added the company.
CosterEco system is a unique technology designed to address these issues: thanks to the interaction of a special insert, valve and actuator, delivery rates and spray performances are kept stable until the total emptying of the can.
CosterEco can be employed with any alcohol-based spray product, and it has already been tested with several cosmetics such as perfumes, body deodorants, water mist, and air fresheners.
"We decided to accept the challenge that the market was launching: to create a new technology that would allow us to maintain our sustainable essence,” stated Alfeo Tecchiolli – Coster’s discovery and innovation manager.
"We strongly believe in sustainability, and we think it is the key driver for innovation in every application. With CosterEco, our goal is to provide customers with an eco-friendly spray experience without giving up on performance."
He added: “The next steps will be to increase the range of applications and formulations covered, even with powders and resins, making compressed air potentially suitable for any product. We have already carried out a large number of internal tests together with customers’ bulk obtaining very positive results, and many other projects are already ongoing. Now we are ready to help more and more brands to extend their line adding products propelled by air."
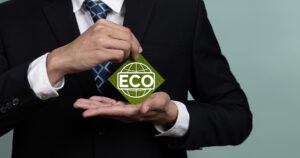